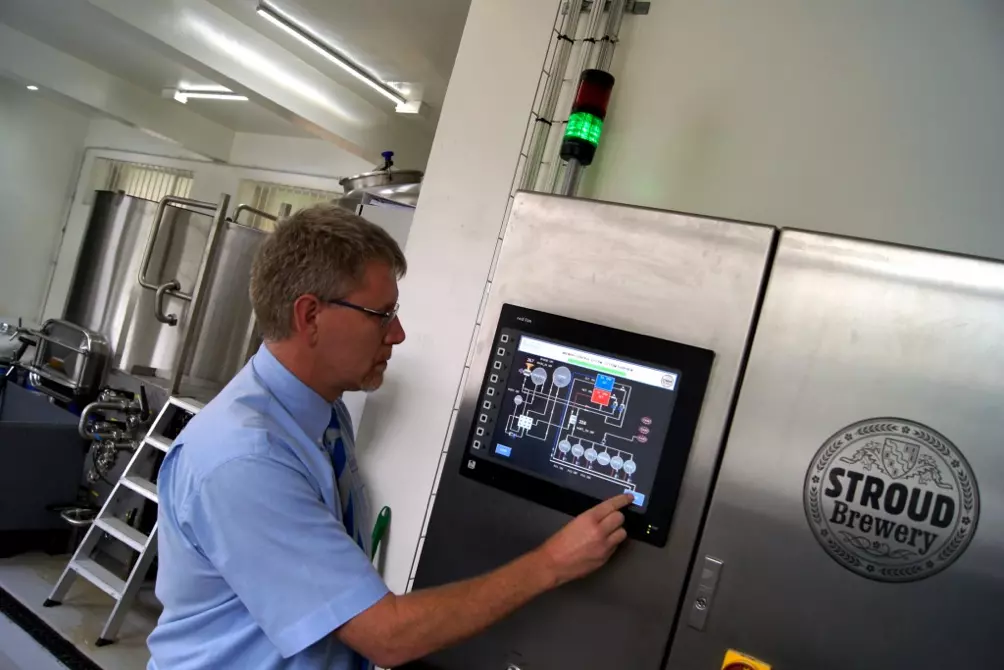
What is the purpose of flow measurement?
Flow measurement is used across many different processing industries, from food and drink manufacture to pharmaceutical and oil and gas processing. In some manufacturing processes, such as pharmaceuticals, flow measurement is used to ensure that the right raw ingredients are mixed together accurately and at precisely the right time. In other areas, such as oil and gas or the production of alcohol, flow measurement has a direct impact on the bottom line. Within the oil and gas industry, there are also extremely tight regulations, and therefore businesses in these sectors often have entire departments dedicated to metering and measurement because it is critical that they meet the stringent demands of industry regulatory bodies. We take a look in this article at the theory of flow measurement, how it is applied across many different industries and some of the more common flow measurement solutions, such as the coriolis flow measurement principle.
What is a flow meter used for?
Flow meters are used for the accurate monitoring of liquid or gas flow. They can be used to measure either the mass or the volume of a liquid or a gas. In most industrial processing plants, the basic purpose of a flow meter is to maintain efficiency and accuracy within the plant and to understand and influence profitability.
What is the basic theory of flow measurement?
The vast majority of flow meters use the fact that the cross-sectional area of a pipe is a constant, which means that if you measure the velocity of the liquid inside that pipe, you can use this to calculate an inferential flow rate. Therefore:
volume flow = area x velocity
Why, then, are there such a wide variety of flow measurement devices on the market and a concern about using the right one for your application? Because the type of flow measurement device selected is critical and must be suited to the environment, the application and the type of flow that needs to be measured. For example, contaminants or solids within a flow can disrupt some types of flow meter. Additional phases within the flow can influence the measurement, secondary instrumentation are sometimes needed to complete the measurement process, and the correct installation and calibration of the equipment can be crucial.
Types of flow measurement
One of the most common types of flow measurement is the Coriolis device. The Coriolis flow measurement principle is based on the use of motion mechanics and uses the vibrations made by the flow of the liquid to assess the mass flow. A Coriolis flow meter contains a tube that is caused to vibrate at a non-harmonic frequency. When a fluid passes through this tube the momentum of the fluid mass causes the frequency of the tube’s vibration to change. The tube will deform slightly, causing a measurable phase shift which is directly proportional to flow.
An alternative but extremely effective option for use in hygienic environments applies surface acoustic wave (SAW) technology to the theory of flow measurement. The FLOWave flow meter developed by Burkert requires no contact with the flow itself, and all the elements used to measure flow are contained on the outside of the pipe. This means that, unlike when the Coriolis flow measurement principle is applied, there is no risk of pressure drops or leakage and no dead spaces. The reason that this solution is ideal for hygienic applications is that the lack of contact with the flow means that there is no risk of contamination – of either the fluid or the measurement device – and CIP and SIP cleaning techniques can be used without concern for the flow meter itself.
For more information on the Burkert FLOWave flow meter, get in touch with the team at BM Engineering on 0141 762 0657 or email sales@bmengineering.co.uk.