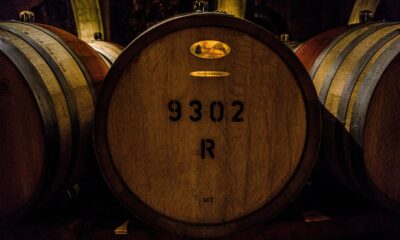
Flow measurement in the brewing industry
With the UK’s brewing industry showing a turnover of nearly £9bn with 28m barrels sold each year, that means the average consumption per person is 71 litres a year. That’s a lot of beer – and with the number of microbreweries and small independent brewers growing annually for a number of years in recent times, we have ended up with a thriving industry and over 3,000 breweries in production in 2020.
Why is flow measurement in brewing an important part of the process?
Brewing is a balancing act of raw materials and biological processes to produce beer of a specific alcoholic strength, taste, colour and aroma. If any of these materials or processes are outside of specification then you end up with a product that is unrecognisable, or at worst, dangerous. A batch that doesn’t meet standards can result in its destruction, an extremely wasteful and expensive exercise. Even an ingredient as seemingly harmless as water is critical in the brewing industry as it is a primary product and therefore the quality of the water ultimately affects the quality of the final result. Thanks to modern techniques for flow measurement in brewing, water can be measured and controlled easily, not to mention the amount of water used in the cleaning process, which is now just a fifth of the amount used a few decades ago thanks to better measurement and control.
Different types of flow measurement in brewing
Unlike in home brewing situations, each batch of beer produced in a brewery must be of the highest quality and consistently produced for both taste and profitability. To achieve this, the brewing industry use the highest quality materials alongside the latest in automation and measurement technology. An example of flow measurement in brewing can be found even in the early parts of the process, where a flow meter is used to ensure that low pressure steam or water is added to the malt during the milling process in proportion to the amount of malt being processed and the temperature that it is measured at. Further down the processing line, the mash flow rate is measured to ensure that the quantities delivered to the mash pan and heated up are as exactly as required. Throughout the brewing process, water is used at various stages including the sparge water, which is used as part of the boiling process and is then extracted as steam or condensate. During each of these phases, accurate flow measurement in brewing is essential to the success of the final product and only the highest quality, most accurate and hygienic flow meters are suitable. Of course, there is always a need for a beer flow meter once we come toward the end of the brewing process, and this is used to ensure the correct dosing at stages of filtering, cooling and bottling, as well as the carbonation of the beer using CO2.
The ideal solution for flow measurement in brewing combines accuracy and precision with absolute hygiene. This is why the Burkert FLOwave flow meter is such a popular solution. Its non-contact technology means that at no point does the flow meter come into contact with the media flow to contaminate it, and the beer flow meter itself cannot be compromised by the flow of media or any SIP or CIP process used between batches. Because all the elements of the FLOwave flow meter are held outside of the pipe, there are no dead spaces and no opportunity for pressure drop, ensuring that the flow isn’t interrupted and that the readings are accurate and reliable.
For more information on Burkert’s FLOwave flow meter, contact the team at BM Engineering who will be happy to talk you through the beer flow meters available and which ones might be best suited to your application. Telephone us now on 0141 762 0657 or email sales@bmengineering.co.uk.