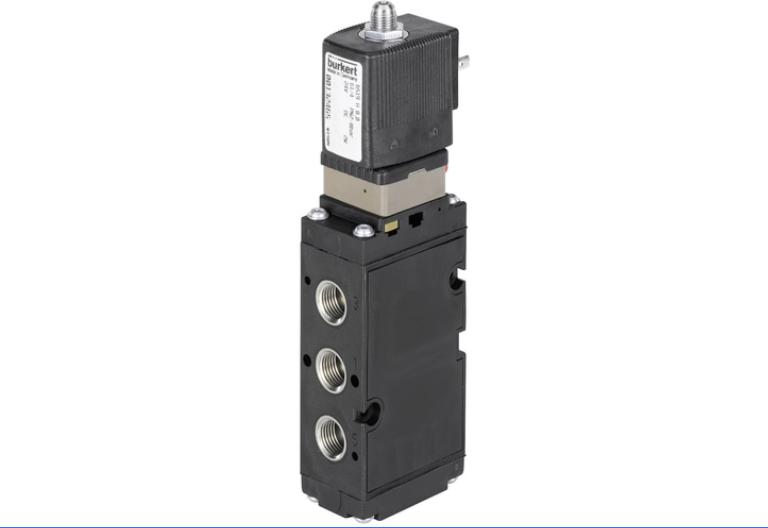
Electric vs. Pneumatic Valve Actuators: Which Is Best For Your Application?
A valve actuator is a mechanism for opening and closing a valve in an application. Before automation, a valve actuator would be a person, manually opening and closing a valve as required. These days, power-operated valve actuators are available to open and close valves in a system without the need for (too much) human intervention.
In this article, we’re going to look at electric vs pneumatic valve actuators and try and answer the question: which one is best for your application?
Electric vs. Pneumatic Valve Actuators
The key point of difference between these two actuators is how they are powered. As their names suggest, electric actuators use electricity, whereas pneumatic actuators use compressed air to power them, though there is some electricity needed as part of their system.
Generally speaking, electric actuators are more expensive to buy and maintain but offer higher levels of precision, whereas pneumatic valve actuators are cheaper overall, but lack very high levels of precision movement. There is, however, a bit more to it than just this comparison and getting the right one is not only crucial to the running of your applications but has wider implications on your business too.
There are a number of different reasons why actuated valves are used in an application, such as the remote location of the valve, the valve’s size, the need to synchronise multiple valves, or even security reasons to prevent potential misuse.
At BM Engineering, we stock a wide range of high-quality quarter-turn actuators which suit many valves, including ball valves and butterfly valves. We also have the ability to add control and indication features, such as position feedback and Namur solenoid valves.
Which one is right? That depends on what you’re using it for. Let’s have a look at the pros and cons of each.
Electric Valve Actuators
Pros
Electric valve actuators don’t require compressed air, so no other systems are required to operate them, assuming there is an electricity supply to your premises. They have generally lower running costs than their pneumatic counterparts and are less intrusive; they take up less space and produce far less noise.
In terms of emissions and sustainability, electric valve actuators win out here. Electric actuators provide more consistent torque through the stroke range, meaning there’s less need for a safety factor when sizing. However, it is still recommended to choose an actuator with a higher torque to provide you with a safety margin.
Finally, a huge benefit to electric actuators is the level of precision they offer. If your application requires a high degree of accuracy, this will be the preferred method over pneumatics.
Cons
The downsides to electric valve actuators is primarily the cost. That low running cost is offset by a higher initial price vs pneumatic actuators, and significantly higher maintenance costs too. They offer a much slower cycle time than pneumatic valve actuators, so this should be taken into consideration also. Finally, though not true of all electric valve actuators, many don’t offer a failsafe. Again, careful consideration should be given to whether or not this is essential in your industry.
What are they suitable for?
Electric valve actuators are sometimes referred to as motorised or rotary valves. They are most often used to operate ball and butterfly valves. They are widely used for fluid transfer in applications, such as irrigation, water supply and heating systems.
Pneumatic Valve Actuators
Pros
Pneumatic valve actuators are generally much cheaper to buy and maintain, not least because they boast high levels of durability, so maintenance and repair is needed less regularly.
They are suitable for applications where space is a commodity – in some cases they are 70% smaller than a comparable electric valve actuator (it should be considered that they will require space for a system to supply compressed air). If you’re working on a plant with hundreds of valves, then you may want to opt for pneumatic valve actuators, as these are much more economical and cost effective than electric valves.
Cons
The cheaper cost and maintenance is offset by the more expensive running costs that come with pneumatic valve actuators. As we mentioned above, the necessity for compressed air means the installation and maintenance of this system, requiring valuable space and money. If you are working with a small quantity of valves then it’s more favourable and sustainable to opt for electric valves.
What Are They Suitable For?
Pneumatic valve actuators operate pushing a piston using compressed air. They fall into two categories:
- Single-acting, which has one port allowing air into the cylinder, which increases in pressure then moves the piston. The piston is then returned to its original position by a spring and the process repeats.
- Double – acting, which has two ports at either end of the piston. Compressed air moves the piston forwards and backwards in the cylinder, with no need for a spring.
Popular examples of applications using pneumatic valve actuators are engines, production machinery and transport systems (such as railway and aircraft systems).
Conclusion
The most important factor is what you’ll be using it for. Be sure to consider the environment in which you need to use the actuator, it will largely dictate what you need.
It’s not a simple choice when choosing between an electric vs pneumatic valve actuator. There are lots of variables that you could, and should, consider. To summarise, it boils down to:
Use: The level of accuracy, working environment (moisture and temperature) , amount of space, medium that the valve is controlling and more, all contribute to deciding which valve actuator you need.
Control: Consider the level of accuracy that’s needed in your application. How much force do you need to manage and deliver? Is hard-wearing durability a factor? Cycle speed? Choose carefully.
Cost: It’s the bottom line in your business after all. Although you have to opt for the right tool for the job, ultimately your budget could end up playing a part with significant cost differences and longer term running costs to weigh up.
Get In Touch
At BM Engineering, we supply a wide range of actuated valves, from some of the world’s leading manufacturers. For example, Max Air Technology’s MT Series rack and pinion actuators, or Kinetrol’s vane type actuators.
Max Air is one of the leading brands for pneumatic actuators and offers a range of cost-effective solutions for the most complicated flow requirements. Kinetrol’s patented design boasts the most reliable quarter turn actuator on the market today.
To find out more about the range of actuated valves available at BM Engineering, don’t hesitate to contact us today on 0141 762 0657, or email us at sales@bmengineering.co.uk