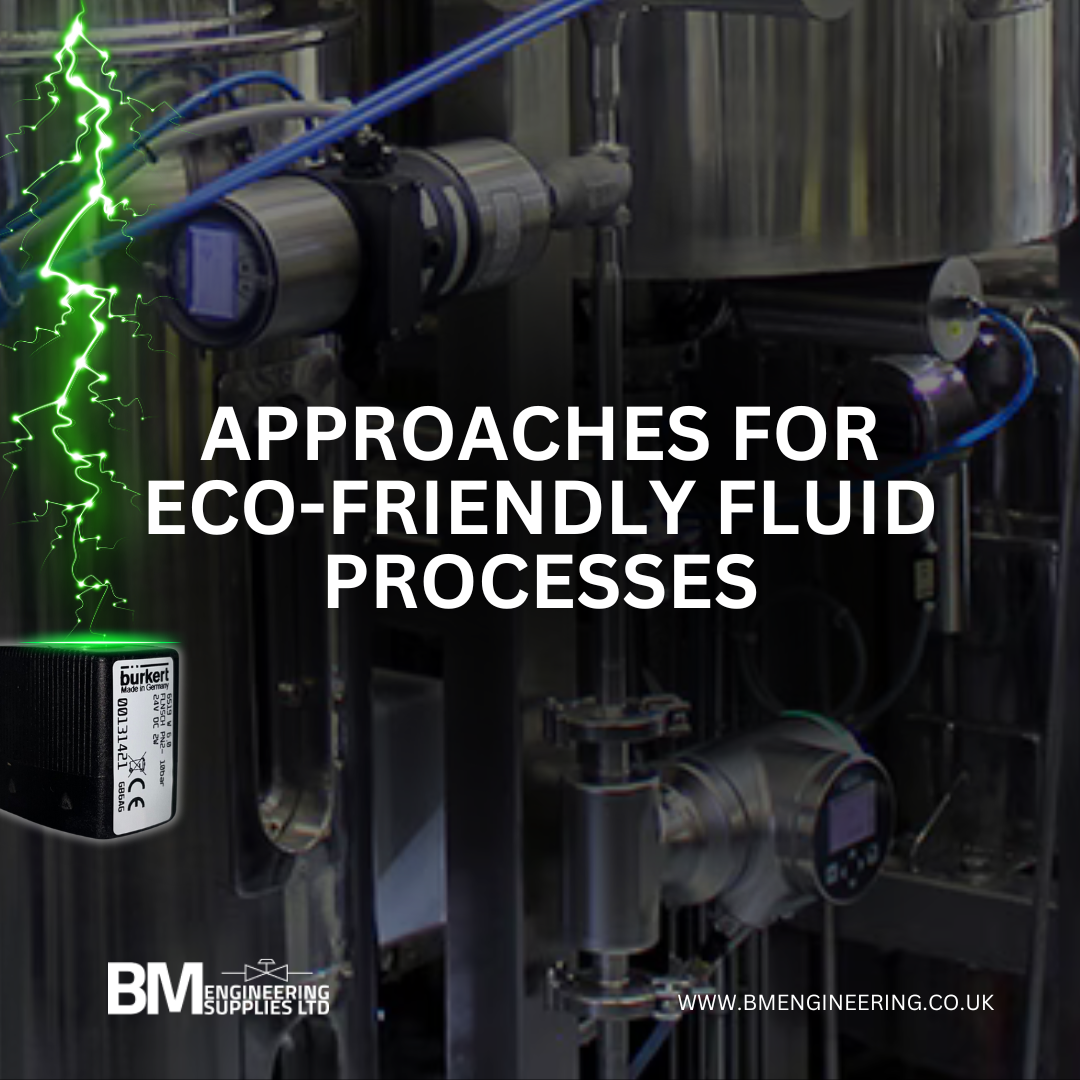
Eco-Friendly Fluid Processes
Approaches for Eco-Friendly Fluid Processes
In today’s manufacturing landscape, while the focus on cost-effectively producing top-quality products remains paramount, the imperative of Eco-Friendly Fluid Processes has gained considerable significance. An increasing number of manufacturers are actively striving to reduce energy consumption, material usage, and waste. Bürkert offers an extensive array of off-the-shelf solutions that decisively address these crucial objectives available to order on our website for example the FloWave.
Kick and Drop Coils: A Game-Changer in Energy Efficiency/ Eco-Friendly Processes
Energy conservation is a significant concern for all manufacturing operations. To address this, our revolutionary Kick and Drop coils provide a powerful solution for achieving remarkable energy savings in solenoid valves. These valves are equipped with two coils: a primary coil to lift the plunger and a secondary coil to hold it in place. The secondary coil can significantly drain power, especially when the valve is left open or in scenarios involving multiple cycles.
The Kick and Drop technology has been meticulously engineered to tackle this challenge directly. It generates an electric impulse to activate the primary coil, opening the valve. After just 500 milliseconds, the secondary coil holding the valve in position seamlessly transitions into low-power mode.. This innovation results in substantial energy savings of up to 80%, depending on the specific application, thereby reducing power consumption, associated emissions, and costs.
Hydroformed Valve Bodies: Revolutionizing Material Efficiency
Efforts to conserve materials have the potential to greatly enhance the sustainability of both the product and its intended application. A prime example of this approach can be seen in Bürkert’s hydroformed diaphragm tube valve bodies.
Traditionally, tube valve bodies are cast, forged, or occasionally milled in stainless steel, resulting in a bulky design to accommodate high pressures. However, these conventional processes entail a significant consumption of stainless steel, which is highly energy-intensive to produce.
In contrast, our utilization of hydroforming involves pressurizing a tube filled with water-oil emulsion within a mould to craft the desired shape. This method requires markedly less material while preserving the original thickness of the tube, ensuring its suitability for high pressures without the need for a bulky design.
Foremost in hygienic applications, a tube valve body with less mass also offers rapid, energy-efficient sterilization. Utilizing steam injected at temperatures ranging from 100°C to 140°C, the valve can be swiftly sanitized. In contrast, a bulkier design necessitates more time and energy to heat up. By contrast, a low-mass Bürkert tube valve body heats and cools rapidly, delivering energy savings and expedited resumption of operations.
TwinPower and Latching Valves
For valve operators looking to optimize energy usage, Bürkert’s TwinPower valves provide a significant advantage. Perfect for valves that remain open for extended periods without requiring an emergency position, TwinPower technology utilizes one coil to move a plunger or rocker into position and another to move it back, resulting in substantial power savings and reduced energy usage. TwinPower technology is featured on valves such as the Type 6724 and 6624.
Latching valves use only a single coil to move the armature and don’t require continuous current to stay in position. To move into another position, the voltage polarity is reversed, with the use of pulses further reducing energy consumption.
Electromotive Valves
The motor-driven electromotive process valve, Type 3361, offers sustainability benefits over large pneumatic valves by eliminating the need for pressurized air and reducing maintenance costs. Additionally, it remains fixed in place due to internal gear mechanisms and utilizes a supercapacitor to move the valve to a safe position in case of a power failure, all while consuming less power compared to a battery.
Valves for Hydrogen Fuel Cells
Bürkert offers ready-made products for clean energy applications such as hydrogen fuel cells with the Type 6440 safety shut-off and Type 6020 proportional control valves, specially designed for Proton Exchange Membrane (PEM) fuel cell systems or Alkaline Fuel Cell (AFC) systems. These valves are constructed with 316 stainless steel and feature low leak rates and a high operating pressure range.
We are excited to offer a range of hydrogen valve types. Understanding the varying conditions of hydrogen, from high to low temperatures and pressures, we emphasize the importance of tailoring solutions to specific needs for example the Zwick Butterfly Valve range.
INOXPA’s CIP cleaning systems optimize various aspects of the cleaning process:
– Water saving: You can save a substantial amount of water by using a good hygienic design and cleaning balls/spray systems. CIP systems can also include a tank to recover water for the next cleaning process.
– Energy saving: You can achieve significant energy savings by using highly efficient pumps and optimizing the heating system.
– Chemical product saving: Minimize chemical usage by operating with recirculation or return in tanks.
– Time-saving: It’s possible to save time without sacrificing cleaning efficacy by optimizing each stage of the CIP system.
In addition to these, using an INOXPA PIG product recovery system offers benefits such as finished product recovery, waste reduction, and simplification of the CIP cleaning process.
Eco-Friendly Fluid Processes from a Single Source
As a full system provider, BM Engineering Supplies sustainability principles to system design and offers a range of Eco-Friendly Fluid Processes. The components, such as coils or plungers, can be individually replaced, extending the service life of the products and reducing wastage. Furthermore, our solutions facilitate remote monitoring, minimizing the carbon footprint of maintenance activities. Partner with us to achieve a virtuous circle of efficient valve and system design.
Contact us today to explore how we can improve the sustainability of your fluidic process and reduce energy consumption. Visit our online store at www.bmengineering.com/store or contact BM Engineering Supplies today at 0141 762 0657 or via email at sales@bmengieering.co.uk.